All about multi-cavity injection molding for high volumes
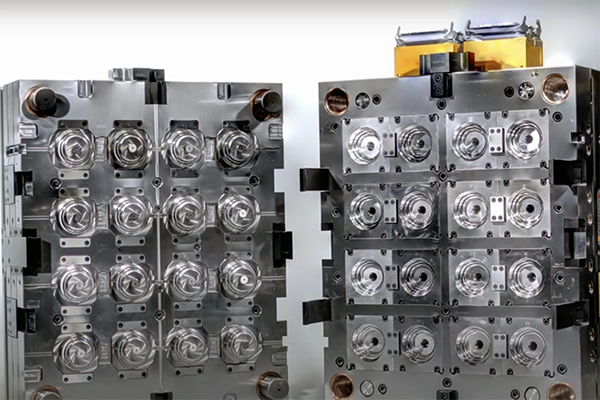
Want to know how to maximize production throughput and reduce costs when making high volumes of plastic injection molded parts? The answer lies with multi-cavity tooling, where it’s possible to produce up to hundreds of finished parts in a single injection cycle. In this Serious Engineering video, Gordon Styles shows you how it’s done.
Surface Textures For Plastic Injection Molding
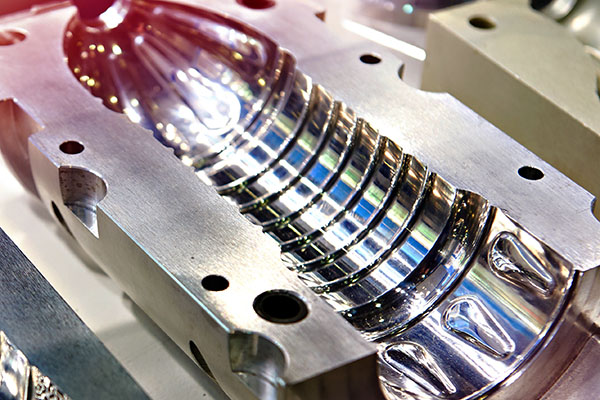
The surface texture of a plastic part influences much more than how it looks and feels. Surfaces can affect mechanical performance, chemical interactions, electrical resistance or conductivity, friction, corrosion resistance, and many other factors. How are these textures created, and why is this important for your project development goals? PIM Surface Texture Surface textures are […]
How To Use DFM To Improve Plastic Injection Molding
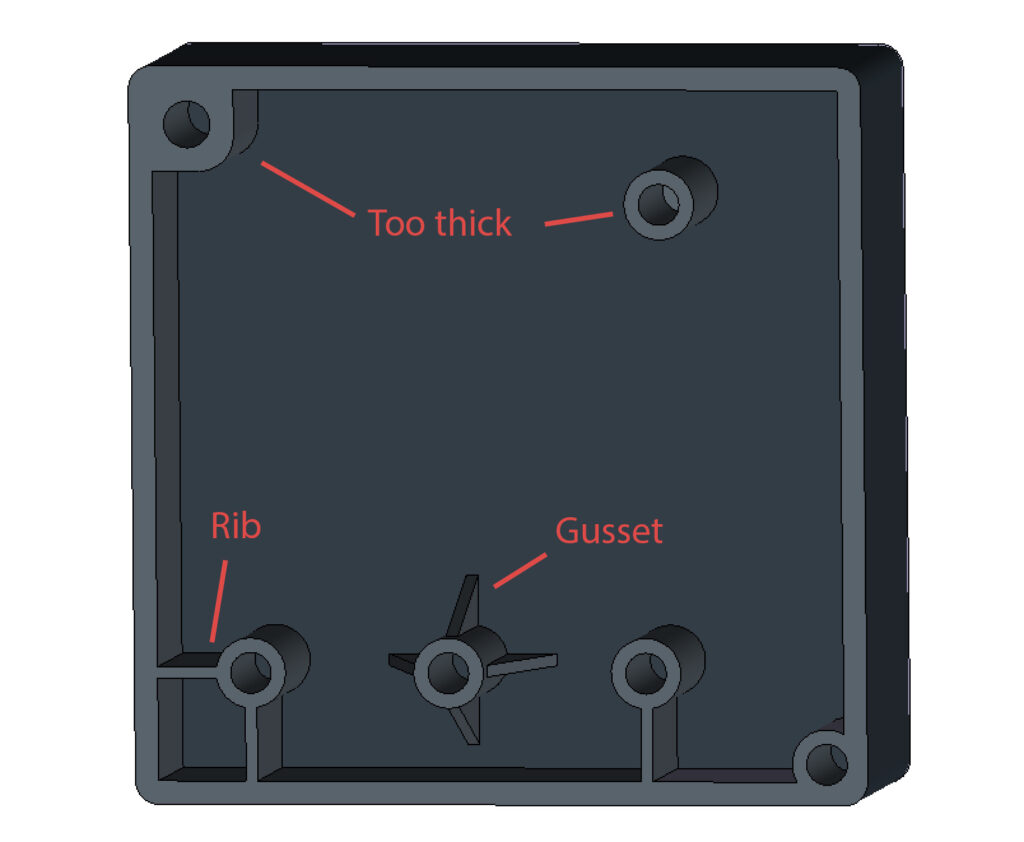
We’ve written elsewhere about the importance of design for manufacturing (DFM) analysis in manufacturing. No matter the size of the project, we always recommend using DFM discipline to save time and money while preserving quality. A complete DFM review covers all aspects of product development. In this study, we are going to concentrate specifically on […]
Understanding multi-cavity designs for injection molding efficiency
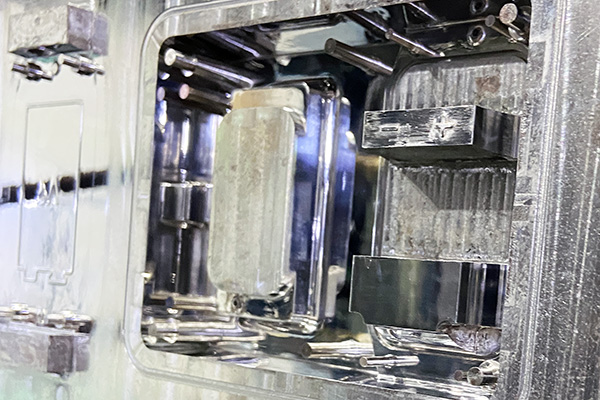
There are three general categories of plastic injection mold tools that product designers can consider when making finished parts. They each have advantages, largely depending on the intended volumes. Let’s take a closer look at which type might be best for your project. A single cavity plastic injection mold tool is the most basic form […]
Color Consistency in Plastic Injection Molding
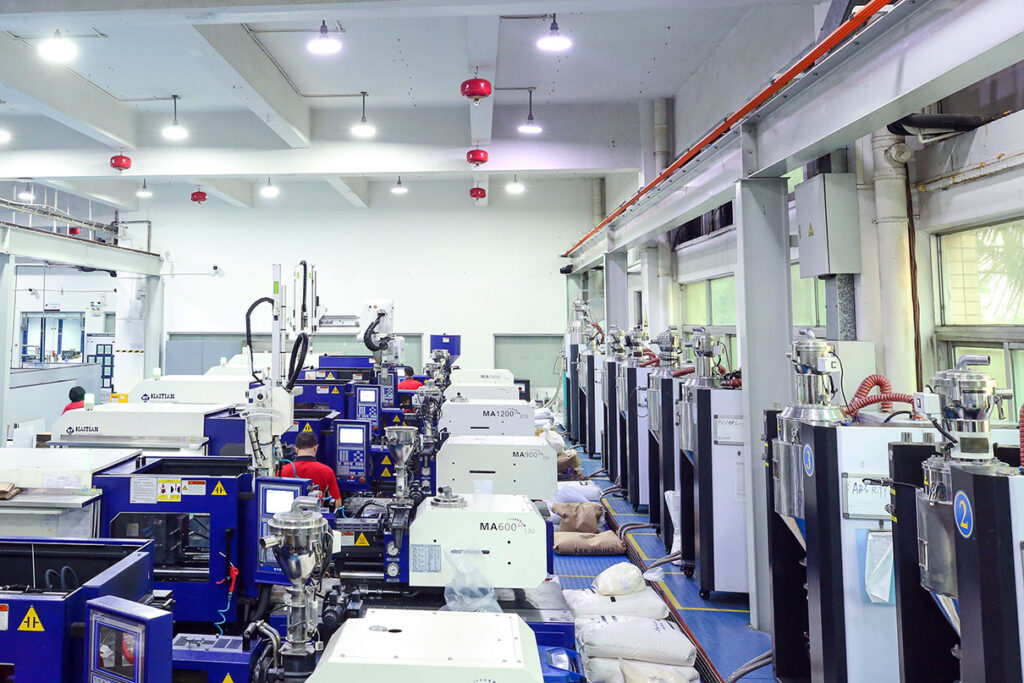
It’s a big challenge to achieve color consistency for large production runs of plastic injection molded parts. To ensure consistency when molding colors, it’s essential that you have careful process control at every step. It’s important to note that plastic color is highly subjective – subjective in how you see and interpret plastic color. It […]
The Top 4 Surface Treatments for Production Tooling
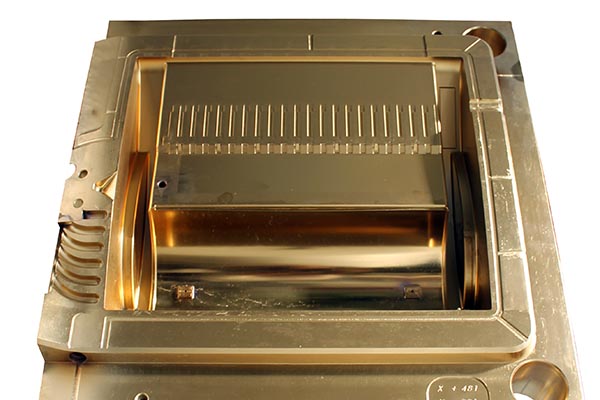
TiN coating on mold tool. Image courtesy of prirev.com.All manufacturing tools are subject to incredibly harsh working conditions and must withstand a lot of wear and tear. Tools used for plastic injection molding are no exception, where corrosive resins and abrasive fibers, injected under tons of pressure, can quickly destroy soft or untreated metal. If […]