Quality Plastic Injection Molding Services
Ready to start your plastic injection molding project? Request a free quotation and design review today
Plastic Injection Molding Services
Star Rapid is a world-class provider of advanced plastic injection molding services. We offer a complete manufacturing solution that covers every aspect of raw material verification, tool making, part fabrication, finishing, and final inspection. Our international team of manufacturing experts is committed to providing you with the highest level of professional support for plastic injection molding services of any size or complexity.
Quality Plastic Injection Molding Services
Plastic Injection Molding at Star Rapid
At Star Rapid we specialize in producing high-quality plastic injection molded parts and mold tools. We offer machining and finishing services to make tools from various materials and can produce 50 to 100,000+ finished parts in a wide variety of plastics. Our international team of engineers and technicians is dedicated to making your custom parts using the most advanced equipment and techniques including Plastic Injection Moulding, CNC Machining, 3D Printing and Vacuum Casting. We’re here to make your product ideas a reality!
Star Rapid
The Plastic Injection Molding Process
Plastic injection molding is the process of filling a mold tool with liquid plastic resin under great pressure. The tool may comprise a single cavity or hundreds of cavities in order to make indefinite numbers of parts. Once the mold tools have been carefully designed and manufactured, the molding process consists of the following basic steps:
- Step 1 – The plastic resin comes in raw pellets. These are dried to the right moisture content, and then if necessary they can be blended with pigments or master batch colorants to create the correct color for the design.
- Step 2 – The dried pellets are poured into the hopper of the molding machine. A reciprocating screw inside the barrel of the machine is used to transport these pellets towards the mold while at the same time heating them.
- Step 3 – Within the barrel, the pellets are mixed and heated until fully molten, forming the liquid resin.
- Step 4 – The heated mold closes automatically and resin, under great pressure, is injected through a gate and into the mold cavity.
- Step 5 – The mold is cooled in a short amount of time to solidify the part inside.
- Step 6 – The mold opens and the part is ejected to begin a new cycle.
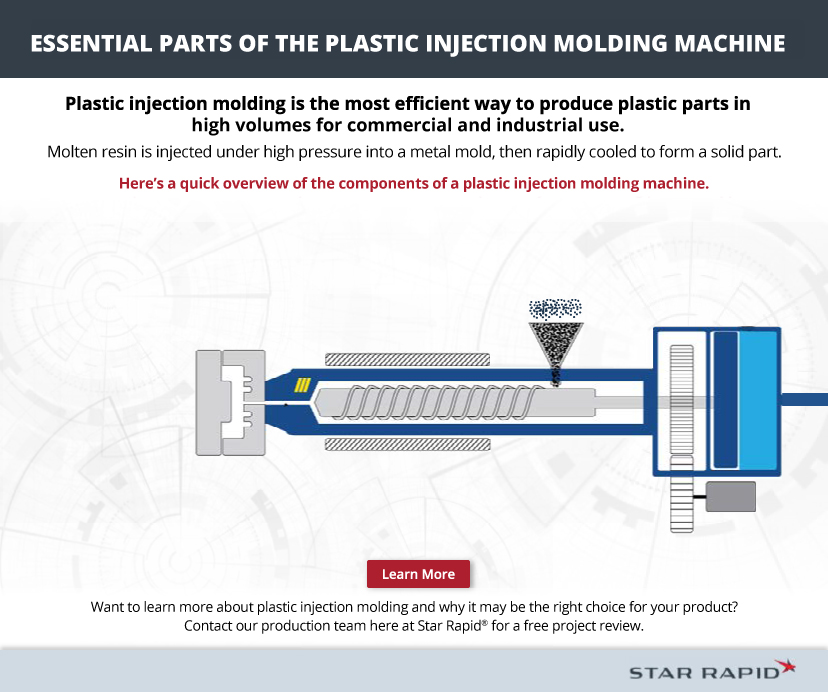
Mold
At the tip of the barrel, a nozzle injects the liquid resin into the cavity of the mold. Once the plastic is then cooled and solidified, the mold opens and the finished part is ejected.
Barrel
The barrel contains the screw and is surrounded by heating bands to provide a uniform temperature to the resin.
Learn More
Want to learn more about plastic injection molding and why it may be the right choice for your product? Contact our production team here at Star Rapid® for a free project review.
Plastic Pellets
Pelletized plastic is first dried and, if necessary, mixed with colored pigment before going into the hopper.
Reciprocating Screw
The reciprocating screw pulls the pellets forward, mixing and melting them as it does so.
Hopper
The hopper feeds pellets into the machine's barrel in controlled amounts.
Want to learn more about plastic injection molding?
Advantages Of Plastic Injection Molding
There are many advantages to plastic injection molding. These include the ability to make large volumes of parts quickly, high surface quality, many resins to choose from, color flexibility, and durable tooling that can last for years.
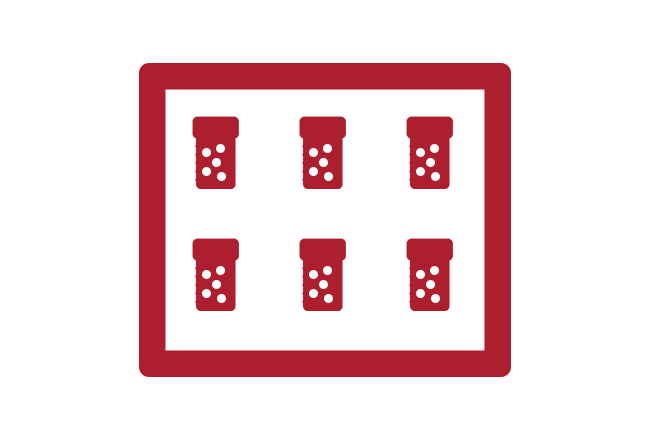
Thousands of resins to choose from
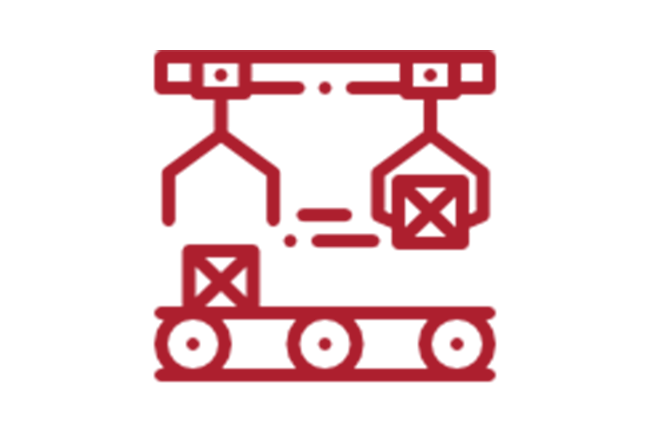
Economies of scale
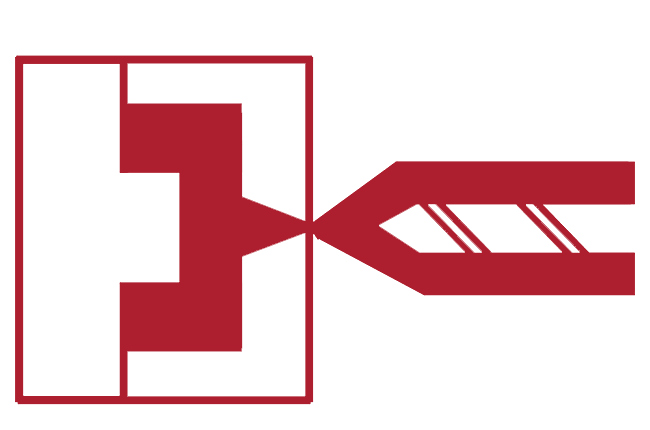
Stable and repeatable
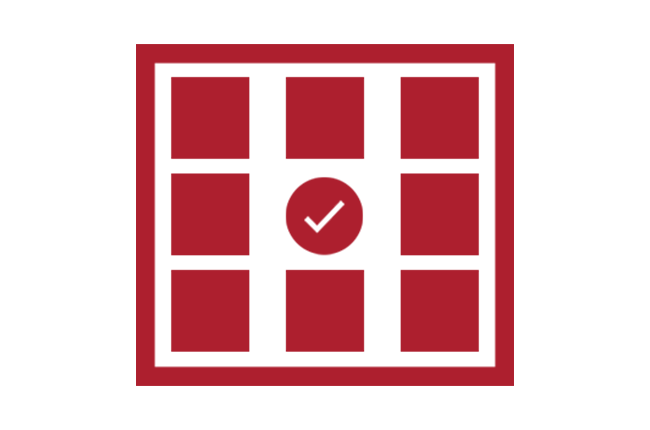
Excellent surface quality
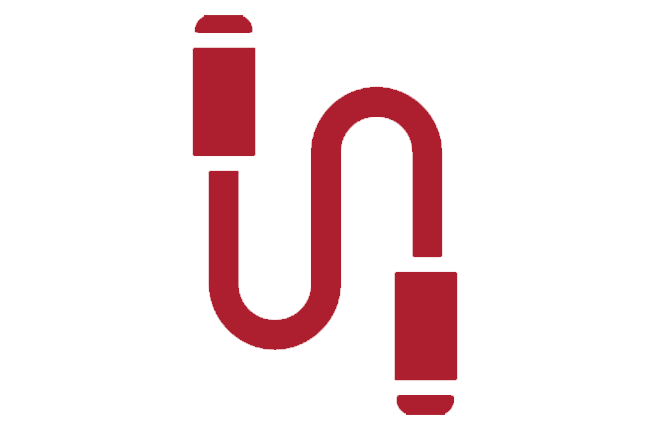
Overmolding for more design options
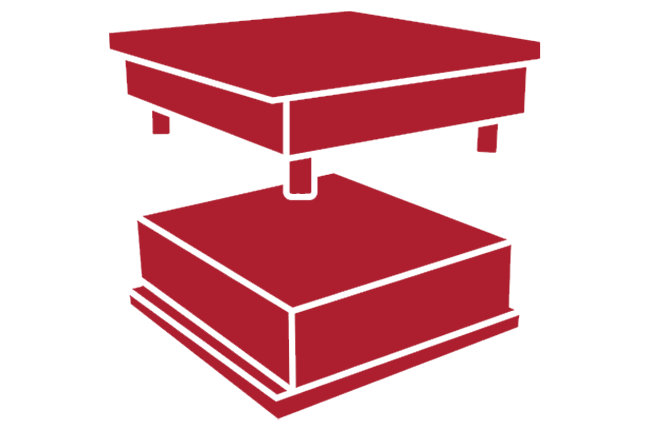
Multi-cavity and family tools
Common Questions
Frequently Asked Questions About Plastic Injection Molding
These are the common injection molding questions at Star Rapid.
Raw plastic pellets are first dried and, if necessary, mixed with coloring agents. Inside the machine the pellets are heated and mixed until the resin is semi-liquid. This liquid is then injected under high pressure through a nozzle and into the gate and runner system of the mold. Resin fills the cavity, forming the shape of the part. It’s then cooled, the part ejected, and the process begins again.
Once a tool is made, plastic injection molding is the fastest and most cost-effective way of manufacturing hundreds of thousands of finished plastic parts. Molded parts have excellent surface finishes with reliable and repeatable dimensional tolerances. And there are resins available to suit most common applications.
Depending on the complexity of the design and possible heat treatment, a plastic injection mold tool can be made in five days to two weeks.
The cost of a plastic injection mold tool can be a significant percentage of the total order for small volumes. However, this cost can be amortized over larger volumes so that it doesn’t become an issue. Rather, plastic resin and cycle times become the main cost drivers for larger volumes.
Why Choose us
Why Choose Star Rapid for Plastic Injection Molding
The finest production mold tools start with quality raw materials, strict process control, and expert toolmakers. Only a supplier with years of experience supporting Fortune 500 companies can ensure repeatable results for your production tooling needs. Here are some of the advantages that Star Rapid offers for high-volume production tool making and injection molding services.
We offer more than just tool making and molding services. Our complete package includes every manufacturing process you need for a total product development solution.
Thousands of companies of every size from around the globe have chosen to work with Star Rapid to help them develop new injection mold tools and finished parts. Your success is the foundation of our reputation.
Your regulatory compliance and your peace of mind are assured with our industry-leading positive material identification department. People trust Star Rapid when the job absolutely must be right.
A comprehensive design for manufacturing review comes with every tool and product design project. You’ll receive superior results while saving time and money.
We support your development goals by having no minimum order volumes or value for our injection molding production. In addition, we have a proprietary AI quoting algorithm that provides fast, accurate, and transparent pricing on every project, every time.
What Our Customers Say
Feedback and reviews from our clients.
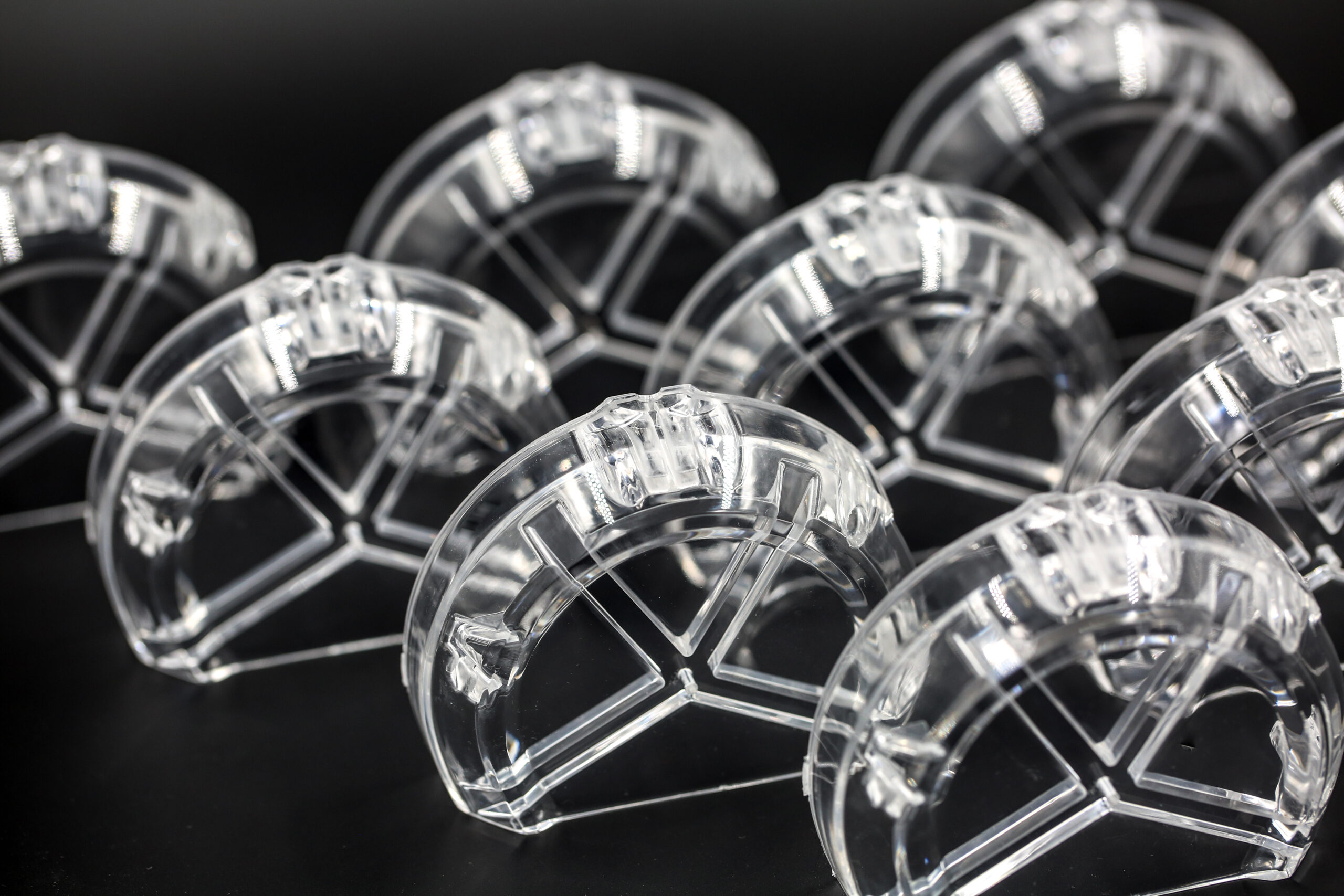
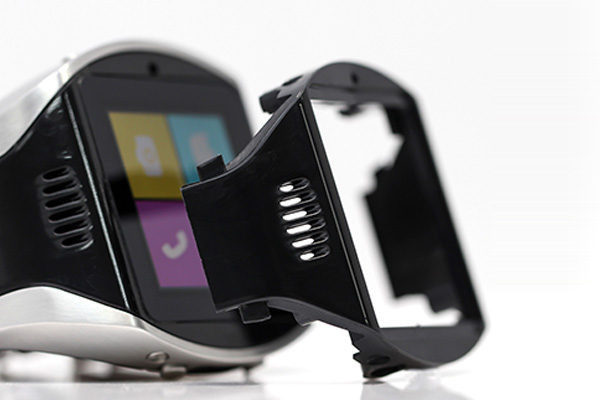
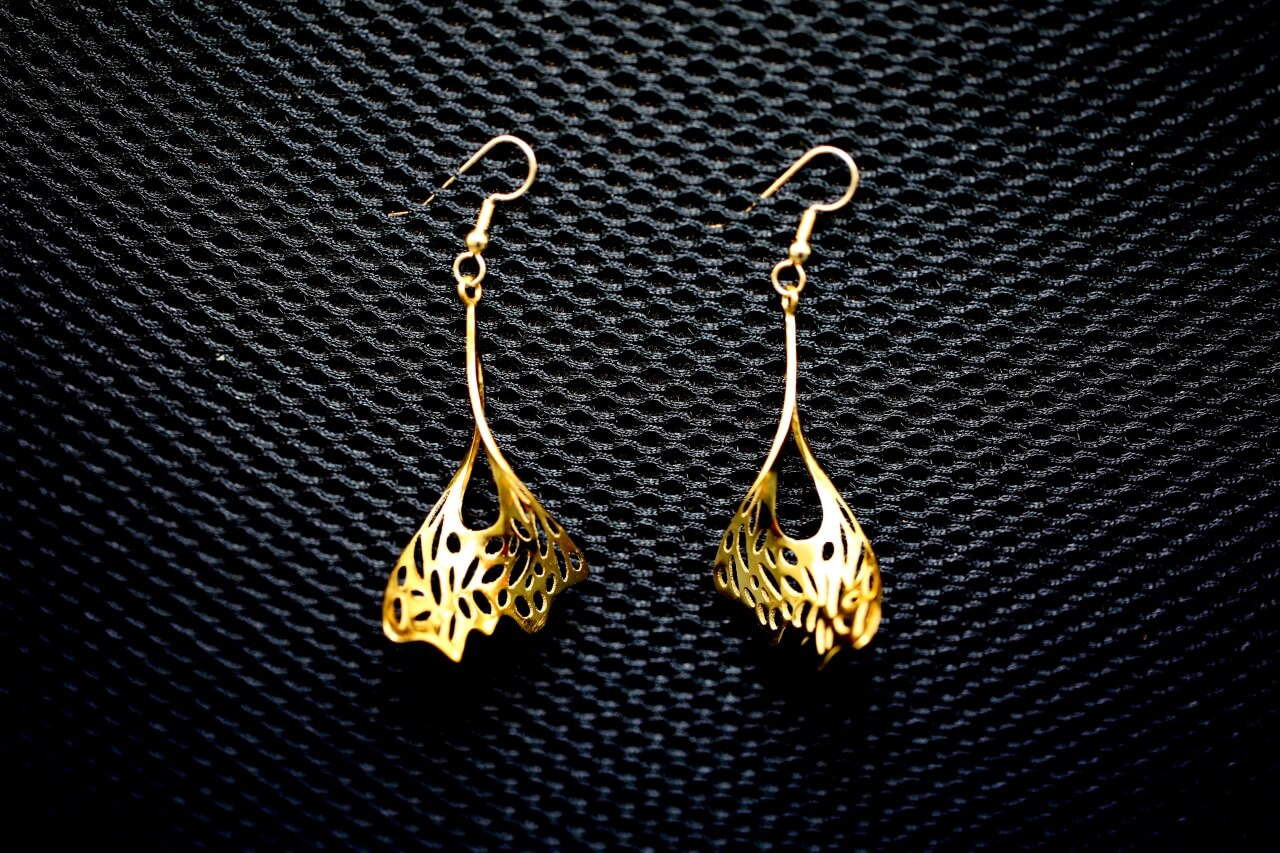
Plastic Injection Molding
Quality Certifications
Proud to be certified by TÜV Rhineland and Dun & Bradstreet to the highest international standards.
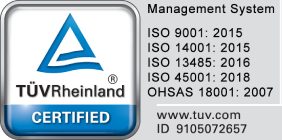
ISO 9001:2015
General quality management system applying to all of our manufacturing services. Because every job is important!
ISO 13485:2016
A more demanding quality management system for products and services related to medical devices. Setting the bar just a little higher!
ISO 14001:2015
International standard for a responsible environmental protection system. Proud to do our part to make a better world!
ISO 45001:2018
Occupational health and safety. To ensure the well-being of everyone in the Star Rapid family!
FAQ
Star Rapid Injection Molding Service FAQ
These are the common injection molding questions at Star Rapid.
This depends on the complexity of the tool design and the type of material the tool is made from. Generally speaking, a very basic square shape made from relatively soft steel such as P20 can be made in less than one week. Very hard steels take longer to cut and to heat treat, while complex shapes or advanced surface textures can require three or more weeks to prepare.
A reputable manufacturer will positively identify all incoming raw materials, and will carefully control every stage of production to ensure process repeatability. Full ISO certification is a good demonstration of their commitment to excellence.
A product developer should be looking to save money on the cost of a mold tool. In most cases, a less expensive tool is going to be of poorer quality, less durable, with looser tolerances and a bad surface finish. These are not cost-savings. Instead, they’re expensive mistakes. Rather, savings can be made long-term through production efficiency, fast cycle times, and process stability. As volumes increase, the relative cost of the tool goes down until it’s almost free.
Our molding service is strengthened by our extensive expertise and a wide range of production capabilities. Our industry-leading facilities allow us to handle projects ranging from micromolding (10 tons) to large projects over 500 tons. This means we’re capable of producing parts ranging from millimeters to cubic meters in size. Our production of such a wide variety of parts enables us to best meet your needs. Further, we have unique access to tooling experts with decades of experience. They are available for video conferencing and customer support. We’re united in our efforts to help you have a satisfactory injection molding experience!
We make tools and dies from S136H, 2316H, H13 hardened, 2316H, P20, 8407, and NAK80 semi-hardened steels. We offer standard SPI finishes, EDM texturing, and several different types of etched textures. We also have thousands of thermoforming plastics available – contact us for details.
All orders are carefully reviewed by our tooling engineers to provide design for manufacturing optimization. We also work closely with outside design consultancies who can offer expert advice on the process of moving a product from the concept stage to production-ready.
Our quality-control system includes several steps to ensure safe, high-performing products for our clients. As with all of our services, we conduct comprehensive material verification and testing before molding begins. This includes the metal used in our molds and the plastics used in production. During production, we carefully control all processing conditions — including temperature and humidity — to maintain repeatable results. Many molding companies neglect to do this, which can lead to flaws in the finished parts. We also 3D scan complex shapes to ensure accuracy.
Applications for Plastic Injection Molding
Proudly providing high-quality prototyping and manufacturing services.
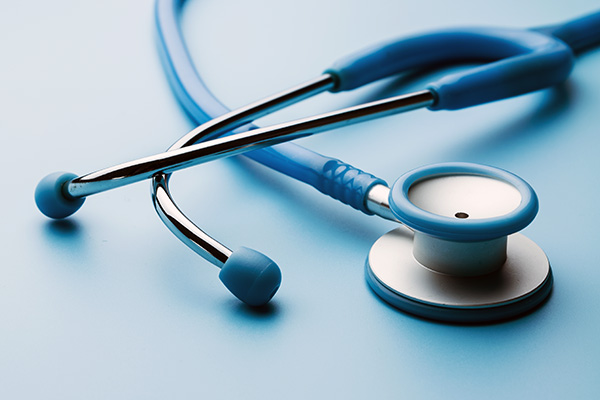
Plastic is very useful in the medical field. Resins are lightweight, non-toxic, inexpensive and can be reused or recycled. Applications include syringes, catheters, dispensers, tubing, and other appliances. For more information about plastic injection molding in the medical field, read our blog post.
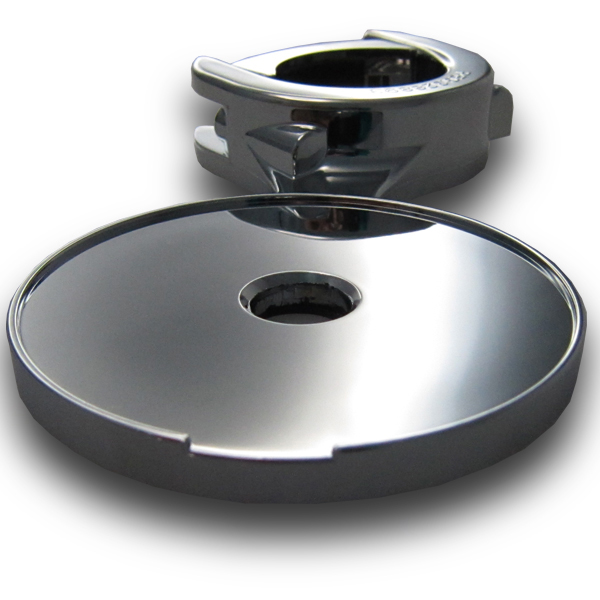
We use plastic every day for work and play. Plastic compounds with different chemical properties are found in computer keyboards and mice, game controllers, headphones, toys, home appliances and kitchen gadgets – anywhere you look. Learn more about plastic used for consumer products.
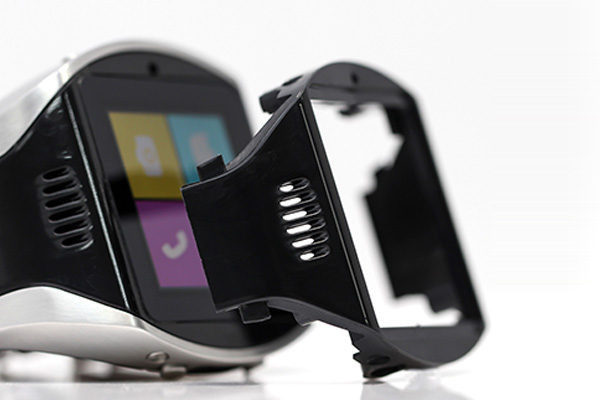
Components like circuit boards, switches, wires, batteries, and sensors must be placed in strong, lightweight, non-corrosive, and non-conductive housings to protect them while also safeguarding the user. Learn why plastic injection molding is an ideal solution to support the electronics industry.
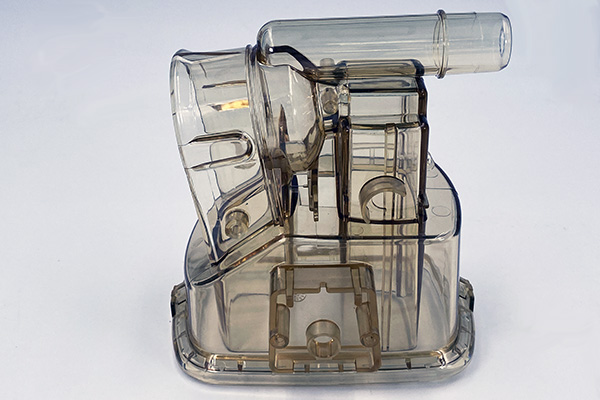
Plastic products used in agriculture must be strong and durable, able to resist UV light and chemicals. Engineered plastic parts are used in conveyor belts, drive trains, feeders, water sprinklers, fencing, tools, and much more. Learn why plastic injection is a great solution for the agriculture industry.
Common Questions
Plastic Injection Molding Tolerances
Plastic resins expand and contract because of temperature, mechanical stress and moisture. Our manufacturing tolerance guide gives you general information on the shrinkage characteristics of most common resin types to help guide your design decisions.
As part of our design analysis, we’ll indicate any areas that might produce thermal stress, shrinkage, warping, or other avoidable defects in your injection molded parts. For more information, consult our manufacturing design guide on common defects and how to avoid them.
Unless otherwise specified, we comply with the DIN 16742 standard tolerances for injection moldings. Ensuring the highest quality is an important part of our production process. Be sure to read about the visual quality standards guide that we apply to injection molded parts.
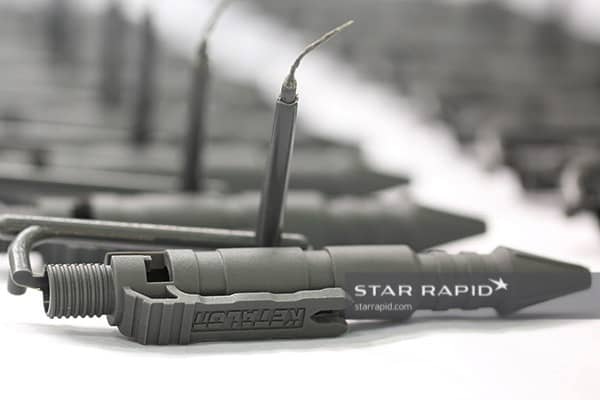
In this Serious Engineering video, Star Rapid CEO Gordon Styles offers some helpful strategies for dealing with weld lines and witness marks on plastic injection molded parts.
In Episode 11 of Serious Engineering, Star Rapid CEO Gordon Styles takes us through a closer look at four of the most common resins used for plastic injection molded parts.
Injection mold tools can be textured to provide a variety of functional and cosmetic features to molded parts. Learn how we do it in this Serious Engineering video.
Plastic Injection Molding Resources
Star Rapid operates a world-class manufacturing facility. Talk to our experts who will help you to make your design ideas a reality.
Some plastic injection molding suppliers offer “automated” DFM analysis, which is necessarily limited to only the most basic part designs on tools with no cooling circuits. This severely limits your design freedom. At Star Rapid, every project receives a personalized DFM review tailored to your exact needs.
Find the plastic injection molding resin that is right for your project.
Careful process control helps us to maintain color consistency. Learn how we do it in our white paper.
The highest visual quality inspection standards are used to verify your plastic injected molded parts.
Learn the best strategies for mitigating sink marks on your plastic injection molded parts.
Follow the product roadmapping journey to save time, money and effort on your next project.
Request Your Free Injection Molding Quote Today
After receiving your drawings, our engineers will analyze your custom plastic injection molding parts right away. We actively work with you to clarify all details before providing a quote that is both economical and accurate.