Steel is one of the most common engineering and building materials in the world, found virtually everywhere in a million common everyday items. Of that steel, a significant proportion is stainless steel, considered to be rust-proof. But not all stainless steels are the same and many people don’t know what exactly makes steel “stainless”. Let’s look at the chemistry of this most useful metal so you can decide which type may be best for your next manufacturing project.
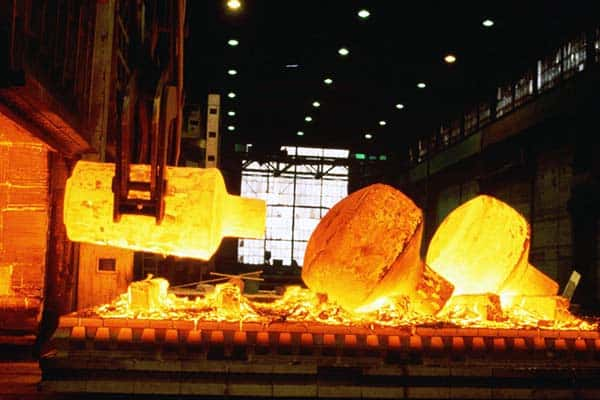
First Of All, What Is Steel?
All steels are alloys, or chemical combinations of many elements. The foundation of all steel is iron. Iron in its pure form is rarely used for industrial applications because it’s relatively soft and brittle and thus not suited for mechanical work. But iron is the most common element in the Earth’s crust so it’s abundant, easy to extract and not expensive.
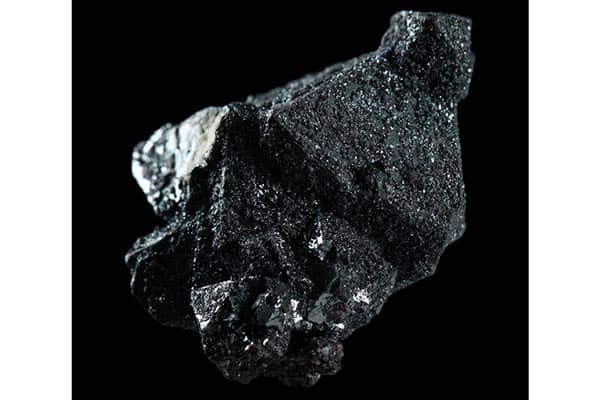
Somewhere in ancient history it was discovered that by adding up to 2% of carbon to iron you get steel, a relatively simple mixture we now call “mild steel.” This discovery really was a revolution, and we’ve been tinkering with the recipe for different kinds of steel ever since.
It’s important to remember that steel has excellent mechanical properties for which there are still no viable commercial substitutes, so steel will be with us for a long time. It’s stronger than aluminum, easily worked, inexpensive, tough and it doesn’t shatter or crack like carbon fiber. But mild steel has limitations, especially when exposed to the environment.
What Is Rust?
One of the most chemically reactive of all elements is oxygen. It loves to join with other elements to create new chemical compounds. When it joins with iron, it makes iron oxide, or rust. This will happen to mild steel very quickly unless the surface is protected with some treatment like painting, glavanizing or powder coating. Each of these surface treatments have their merits but eventually water will find its way in and cause rust. As we all know, rust is not just unsightly but causes the substrate to lose mechanical strength and eventually fail completely.
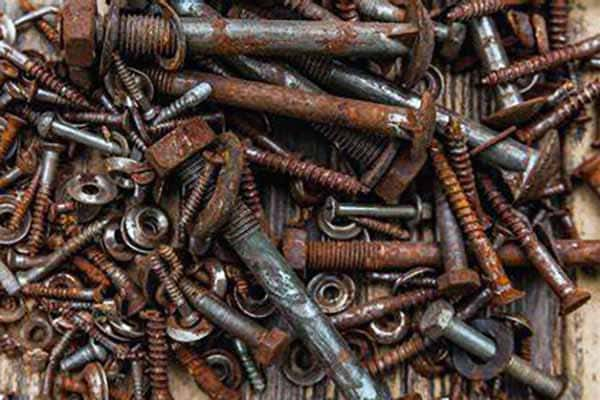
What Is Stainless Steel?
The secret to stopping rust is to prevent oxygen from forming bonds with iron. The best way to do this is to get something else to bind with the iron first. After many experiments, it was discovered that by adding up to 10% of chromium to mild steel you get a new alloy that doesn’t rust – stainless. This innovation, by the way, took place in Sheffield, England in the 1930’s, giving that city its reputation for making some of the finest cutlery in the world.
Stainless is not as tough as mild steel in many applications and it’s more expensive, but it also resists the corrosive effects of water and many other chemicals. Now, metallurgists play with different trace additives like manganese, copper and nickel to get stronger steels that are still rust-free.
How Do We Use Stainless Steel in Manufacturing?
We use stainless steel every day to make finished components via CNC machining and metal 3D printing. Some alloys are biocompatible so they can be used for medical instruments as well as implants and dentrifices.
We also use stainless steel to make tools and dies for plastic injection molding and pressure die casting. There are two main reasons for this. One is that tool steel with higher chromium content, like P20 or NAK80, can take a very nice polish so they produce glossy finishes on the molded parts. And they are resistant to the corrosive chemical attack of some types of plastic resin such as PVC.
What Kind Of Stainless Do We Use?
We can purchase and work with any commercially available grade of stainless steel. For most of our common work we use four main types:
Type 303
Because of its relatively high sulfur content, this stainless steel is softer and therefore is used for most CNC machining work. It is non-magnetic and does not accept heat treatment, so the hardness is not affected by the heat induced via the machining process (work hardening). However, the additional sulfur makes it a little less corrosion-resistant than type 304.
Type 304
Higher corrosion resistance than type 303, it is also harder and tougher. It is a bit more difficult to work (machine) than type 303, but it also makes a stronger finished part. This is the most common type of stainless steel used in manufacturing.
Type 316L
A specialty stainless steel with a low carbon content but more molybdenum. This makes it even more corrosion-resistant than type 304. And because it is low in carbon, it does not carburize or give off heavy fumes when welded. This is often used for marine applications where saltwater might damage other steels. Because it doesn’t produce fumes when welded it’s ideal for metal 3D printing.
Type S136
An especially high purity of stainless steel. It is used mostly for plastic injection mold tools when the molded part needs to be an optically clear plastic lens, because the steel takes a very high polish.
Want to Learn More?
Choosing the right raw material for your next rapid prototyping or low-volume manufacturing job is an important part of getting the performance you expect. We’ll be happy to offer more advice when you contact us or upload your CAD files for a free quotation.
Tagged: