There are many forms of pressure involved in making a plastic injection molded part. We’ve explained the importance of clamping pressure before, so now let’s look at three others: injection, holding, and back pressure.
Why is this important to you? Because balancing these forces correctly is one of the keys to making consistently good parts. Pressures determine finished part quality, cycle times, and ultimately, your cost per piece.
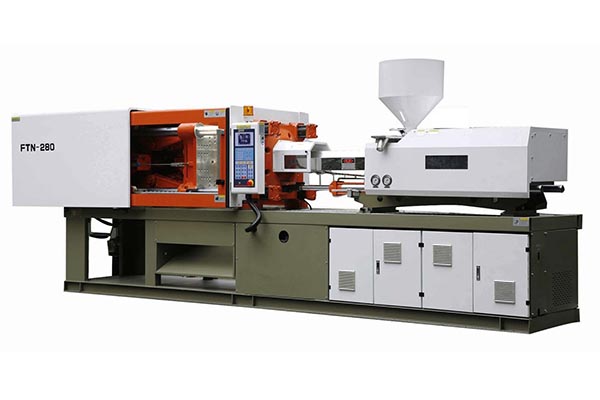
Understanding injection pressure
Product developers want to get as many parts per hour as they can. This is one way to reduce the cost per piece, which is an important consideration for large orders. Because of this, it’s sometimes thought that by merely increasing the injection pressure, you can force the injection molding machine to make more parts faster.
However, there are forces taking place inside the mold that limit this approach. To understand why let’s take a look at what happens during the initial mold filling sequence. During the initial injection, the mold is empty, so there’s little resistance and the cavity fills quickly. But if it fills too quickly it’s possible to cause three types of defects.
- One, the molten resin can spray out of the gate in a jet, rather than flow smoothly. The resin will hit the opposite tool wall, cool, and solidify, making a defective part.
- Two, resin under excess pressure will shear, meaning that the chemical bonds are destroyed and again the part will be defective.
- Three, high injection pressure can force the mold open at the parting line. This creates flashing on the part, but more importantly, it can seriously damage the mold tool. This happens because the mold fills very quickly at first when it’s empty and there is little internal resistance. But when it’s about 95% full, the resistance spikes and so does the internal pressure. To avoid destroying the tool and hurting the machine, the pressure must be scaled back quickly at the changeover point.
When the plastic injection molding machine senses that it has reached the changeover point, it will automatically reduce the injection pressure and then switch over to holding pressure, which performs a slightly different function.
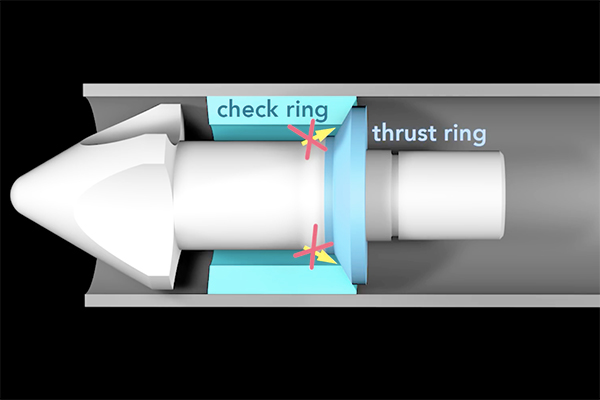
What is holding pressure?
Holding, or packing, pressure is necessary for filling the last 5% or so of a mold tool cavity. This pressure is decreased from the initial injection pressure and held for a longer time for a few important reasons.
For one, trapped gasses in the mold must be given time to escape through vents in the tool. Secondly, packing helps the molecules in the resin to align and achieve their highest density and therefore greatest strength and stability.
Third, thin-walled sections in the part also need time to fill completely, and this can be done by using relatively less pressure over a longer time. And finally, holding pressure is essential, along with good tool design, for relieving stress in the part.
Bear in mind that holding pressure needs to be balanced against another limitation. The cavity must be filled quickly before the gate “freezes off” and becomes blocked by solidified resin. Therefore the process engineer needs to calibrate these forces carefully within a period of time determined by the temperature and chemistry of the plastic.
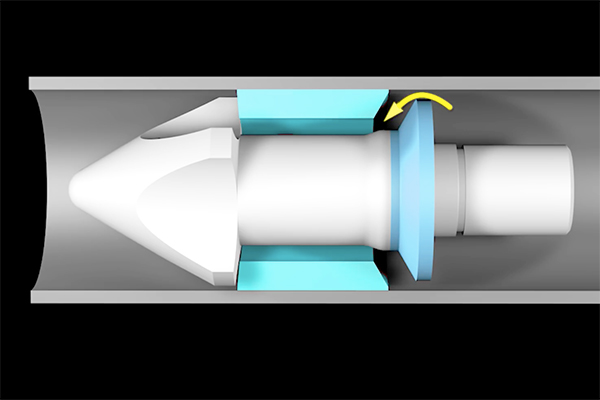
What is back pressure?
During the injection cycle, the reciprocating screw of the injection molding machine is used to plunge the molten resin into the gate and runner system. When the cycle is completed, the screw must retract so that the barrel can be filled for the next part.
Back pressure is resistance in the barrel of the injection molding machine that impedes the return of the screw to its start position. This resistance is deliberate and is created when the operator controls a valve on the machine to restrict the rate at which the hydraulic fluid, which controls the movement of the screw, is returned to the reservoir.
Why is back pressure necessary?
Back pressure is necessary to allow extra time for the heavy flutes on the reciprocating screw to mix the next shot of resin. The cutting action of the flutes heats the resin and maintains consistent density from one shot to the next. They also help to thoroughly mix any masterbatch coloring pigments that are in the resin.
As with the other parameters, this pressure must be controlled by the process technician so that the resin isn’t overmixed, which can degrade it due to excessive shearing.
How do these pressures affect your plastic injection molded parts?
As we mentioned, developers always want to maximize the number of parts per hour in order to reduce production costs. But responsible process control technicians need to carefully balance multiple parameters within the machine to control quality and provide consistency from one cycle to the next.
We’ve learned that higher pressures don’t always achieve faster throughput or better parts. It requires a systematic approach that combines operator experience, good equipment, and optimized tool design.
How does pressure loss affect plastic injection molding?
Even when all of the machine parameters have been set up to their optimal level and the parts are coming out beautifully, that doesn’t quite mean the operator can just walk away from the machine. There are still some things that can happen which must be monitored at all times.
For one, machines are subject to wear and tear. That means that valves can leak or check rings can fail. If that happens it will be impossible to maintain consistent molding pressure. So the machine must be monitored all the time and kept in perfect working order.
Another problem happens when moisture gets into the resin mix. Water vapor, when it’s under a lot of heat and pressure, will of course react as steam and push back against the mold interior. This can make proper mold filling impossible. That’s why proper pellet driers using desiccants are the only way to ensure consistent moisture percentage.
Understanding a little more about how this process works can help you communicate more effectively with your supplier, and also reinforces the importance of good mold tool design.
For more information about plastic injection molding, subscribe to our newsletter to receive industry-related information about product development, manufacturing, and more.
If you liked reading this article, we recommend the following content: